Silicone Bag Infusion Technology
Silicone Bag Infusion Technology
Why is Silicone Bag Infusion Technology preferred ?
- Closed cavity moulding
- Reduces emissions
- Increases production rate
- Increases part consistency
- Uniform thickness across the part
- Improved workforce environment
- Post repair work is reduced
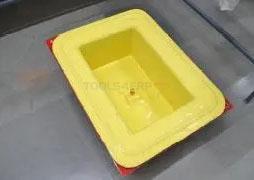
Silicone Bag Infusion Technology (SBIT) Vs Other Closed Moulding processes
Resin Transfer Molding (RTM) uses higher than atmospheric pressure to push resin into closed mould cavity. Uses mechanical methods to seal mould cavity.
Vacuum Infusion Process (VIP) uses lower than atmospheric pressure to pull resin into closed mould cavity. Can use both mechanical and vacuum methods to seal mould cavity.
Vacuum Assisted Resin Transfer Molding (VARTM) utilizes both vacuum and low pressure to transfer resin across closed mould cavity. LRTM is a commonly used process.
Compression Moulding utilizes hydraulic pressure to lower upper tooling to squeeze out preloaded excess resin. Limited to small to medium part size.
- SBIT uses flexible bag instead of upper tooling
- SBIT is least expensive to develop and use
- SBIT is simple and easy to implement
- Reusable vacuum bagging makes SBIT cost effective
- High production volume rate can be achieved in SBIT, similar to LRTM
- No consumable waste in SBIT. Reduces cost of film, tapes, etc.
- Labour reduction in production preparation and post production
Silicone Bag & Mould Setup
- Spray Fabricat rm to precise shape of intended part
- Provides optimum corner compaction
- Bag will not properly fit when lay-up is incorrectly placed
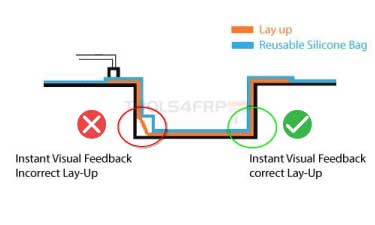
Production with SBIT
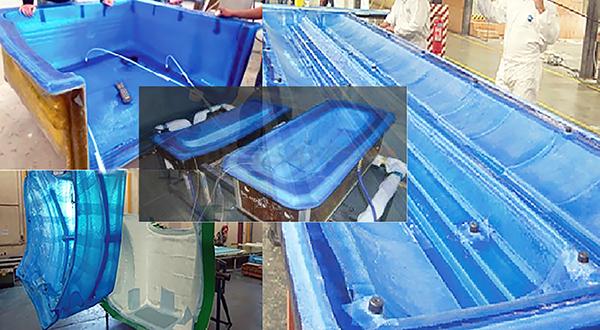
Advantages of Silicone Bag Infusion Technology (SBIT)
- Flexibility to choose different type of fibre reinforcement
- Achieves higher glass content as compared to other close mould process
- High yield per silicone bag, can achieve up to 500 parts
- Environment friendly, no emissions and no wasted consumables
- Get high productivity with less manpower